Packaging Redesign
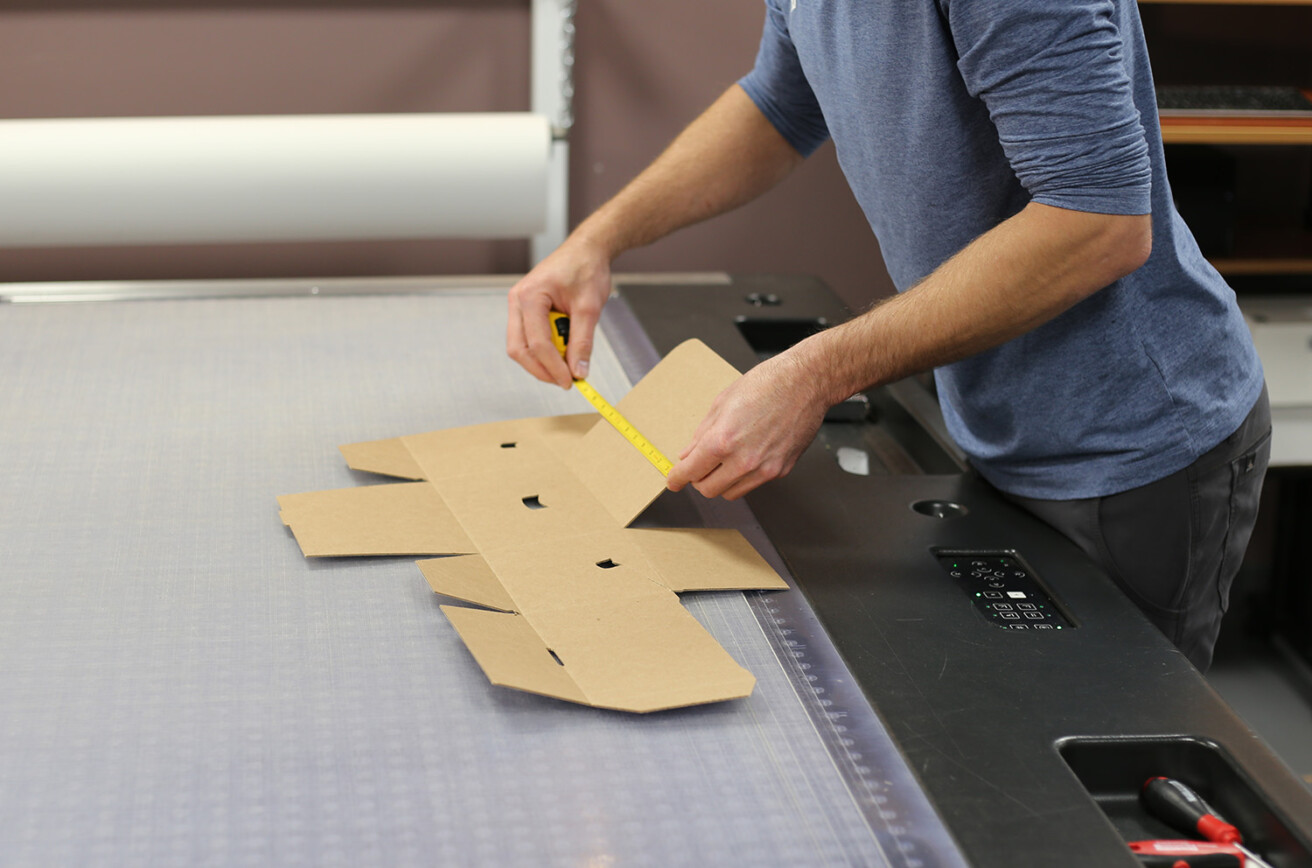
Challenge
There are a lot of different ways to manufacture the same piece of packaging. It’s our job to know what the best option is. Our customer uses telescoping trays (top and bottom trays that fit together) to package their product. They had eleven different size variations of this tray, making 22 different skus. This presented two different challenges. First, this takes up a lot of warehouse space and they need to ensure they are organized properly to match the top and bottom trays together. Second, having that many skus often leads to lower run rates for each. Lower run rates equates to higher piece prices. Using our packaging engineering team we are able to analyze their packaging and come up with a solution that saves them time and money.
Solution
Our team realized that there was no need to be running 22 different skus. Our packaging engineers redesigned the trays to run the tops and bottoms together. Using one of our state-of-the-art rotary die cutters, we are able to run each set nicked together. This lowers the amount of skus from 22 down to 11.
Results
By running the trays nicked together and eliminating 11 skus, we were able to decrease the amount of orders our customer needed to place. While the total cost for one order increased due to the added material, the overall spend was greatly reduced since the amount of time spent running decreased. In addition, running the trays nicked together allows for better organization. When they are ready to be used an employee simply grabs the tray, breaks them apart.